Glass Etching: cream vs blasting
Well another type of project I have been wanting to try since I got my Silhouette Cameo cutter was making vinyl masks to be used in laying over glass object for etching.
Verdict: blasting wins hands down IF you can do it, have the space/cabinet..etc
I used the ‘air eraser’.. and the media sold at HF. (my kit even came with a little bottle of it).. but I bought a bigger one for $10.00
It’s the stock aluminum oxide 220 grit I think
http://www.harborfreight.com/2-lbs-220-grit-white-aluminum-oxide-abrasive-66846.html
HarborFreight being the mess that it is.. actually has/had two kits when I went there..
A bunch of this one:
that look like nothing more than the gun & hose..
and waaaay in the back I saw a different box, which looked like real ‘kit’.. gun, hose, bottle of al. oxide abrasive, wall mount/hook, and crap-tastic face mask..lol
red body vs body gun for ‘quick’ sign of different kits.. (and part numbers)
according to HF though.. 1 or both are discontinued? (so who knows.. they don’t know much over there)
decent purchase for under $20.00USD … probably not as quality as more expensive ones.. but it works.. sometimes a quick shake to unclog media, but got the job done none the less.. J
As for the two etching styles I tested:
here is the cream I tried initially..
at first I thought the cream results were “OK”..
I had read about the non-uniform finish.. (lighter/darker/patchy in some areas..etc)..
I got the same thing()s/results.. however.. to be fair.. Im not sure if I didn’t have a CLEAN glass/surface to begin with.. or maybe some of the ‘stick’ (residue) from the painters tape/transfer paper was left on the glass in certain areas? Oil from fingers?.. using a cream, ALL of that can affect it… so I don’t want to blame it ALL on the cream
So I was like ‘meh’ (might have potential if I can be more careful., was definitely easy & fast and required little prep/clean-up..etc)
RESULTS:
**I put the cream on fairly THICK.. and left it on for 4+ minutes.. (the recommended time is 60 seconds)
When I tried the blasting method.. the results were MUCH better and, if can be done, is the method “I” would choose/do every time.
Darker, more uniform ‘etch’ is left.. decent edges as well.. (even on the 10+ font at bottom)
RESULTS:
overall the blasting is BEST IMHO… but the cream ‘does’ work ok. Its great to be able to have this ability/option now..
Silhouette Cameo + etching cream/air eraser + Dollar Store = great, cheap gifts!
Another SMT stencil cutting post….
Finally some results!
I recently purchased a Silhouette Cameo (http://www.silhouetteamerica.com/?page=shop&cat=1)
Aside from all the things that can be done with this machine (cut fabric, vinyl, paper/card stock, etching plastic, cut cake fondant, stickers, signs, wedding cards/invitation, and the list goes on and on...) one of the things I wanted most was to be able to cut SMD/SMT stencils for making pcb's at home.
It has been a 'trend' lately, seeing the idea pop-up on HackADay , IdleLoop, DangerousPrototypes, and other blogs/forums.. so I decided to get to work on what it woudl take for me to produce the same results.
First I want to give a shout out and credit to several people/places as nothign I have done here is 'new' or innovative, its just the results from the hard work and sotware of other people, who decided to share with us, for this purpose.
HackAday, Idle Loop, DangerousPrototypes, Pmonta, teletypeguy, jessuscf...and everyone else I forgot..
http://hackaday.com/2012/12/27/diy-smd-stencils-made-with-a-craft-cutter/
http://www.idleloop.com/robotics/cutter/
http://pmonta.com/blog/2012/12/25/smt-stencil-cutting/
http://dangerousprototypes.com/2013/05/17/cutting-stencil-using-a-silhouette-cameo/
(Im sure there are others.. but these were mains one..and they all link to each other or have a list of links in the articles themselves to oter relevant info)
With that out of the way..
the general overview of everything I have tested and read basically boils down to, there are only to 'viable' approaches that are worth the 'effort'.
Approach 1: Involves exporting a .dxf file directly from SoftCAD Eagle pcb design software, and you inturn import that .dxf file into the default Silhouette Studio software that comes with you Silhouette Cameo.
This is the approach outlined here at:
IDLE LOOP - http://www.idleloop.com/robotics/cutter/
by Cathy Saxton
The ULP script is located here on github: https://github.com/SWITCHSCIENCE/ssci-eagle-public/blob/master/cream-dxf.ulp
(not sure of the author..sorry)
* Dont forget to turn off "scale to fit" for DXF import in your Silhouette Studio preferences.
This is by far the EASIEST approach one can do/try... (its not much different than using your Cameo to open/cut any other .dxf file at this point.
However.. the results were 'ok' (at best!).. and with soem tweaks 'usable' probably with some 'fixing' afterwards..
I experienced the same results as many others on the net have experienced..
not 'straight' cuts.. bowed out box lines, alignment problems..etc
Results: 'ok'.. probably 'usable', maybe with some fixin'/clean-up..
better than a toothpick and doing it by by hand I would imagine.
Next up is the GerberToGraphtec approach. This works DIRECTLY with the gerber file exported from your design software..
and is Python based...
This script/project is by: Peter Monta
http://pmonta.com/blog/2012/12/25/smt-stencil-cutting/
Github files: http://github.com/pmonta/gerber2graphtec
Being on Windows. this was a bit of a learning curve, and require the installation of several supporting apps.
(and not to mention I'm pretty much command line retarded)
Anyways.. download and install these app sin their default locations:
Python 2.7.5: http://www.python.org/
Gerbv 2.6.0: http://sourceforge.net/projects/gerbv/files/gerbv/gerbv-2.6.0/
pstoedit 3.61: http://www.pstoedit.net/
Ghostscript 9.07: http://www.ghostscript.com/download/gsdnld.html
As mentioned here: http://dangerousprototypes.com/forum/viewtopic.php?f=68&t=5341#p51495 in a post by: jesuscf..
he mentioned, for WINDOWS USERS.. we need to edit the gerbertographtec file.. (from what I have read it 'just works' for Linux and Mac.....figured I'd mention it to make you guys happy)
Download the .zip file and extract the folder inside...
Find the gerbertographtec file and edit it as follows:
1.) add the .py extension to the file name (to be able to run the program directly from a command prompt)
2.) Change these two lines:
os.system("gerbv --export=pdf --output=%s --border=0 %s" % (temp_pdf,input_filename))
os.system("pstoedit -f pic %s %s 2>/dev/null" % (temp_pdf,temp_pic))
to:
os.system("\"C:/Program Files (x86)/gerbv-2.6.0/bin/gerbv\" --export=pdf --output=%s --border=0 %s" % (temp_pdf,input_filename))
os.system("\"C:/Program Files/pstoedit/pstoedit\" -q -f pic %s %s" % (temp_pdf,temp_pic))
*He mentions this is because some of the apps above (gerbv & pstoedit) added their executable folders to the path.
One of the final steps is 'sharing' out your Silhouette Cameo printer, in the Printers & Faxes screen in the Control Panel.
(right click >> sharing & security >> share this printer (name it: Cameo)
At this point, I had some problems with the command line stuff he was posting to use to initiate the process and start cutting:
C:\gerber2graphtec-master>gerber2graphtec.py test.gbr > result.txt
C:\gerber2graphtec-master>copy /B result.txt \\[YOUR COMPUTER NAME]\Cameo
alternate line to use: (not tested)
C:\gerber2graphtec-master>gerber2graphtec.py test.gbr > \\[YOUR COMPUTER NAME]\Cameo
I had tested things as described and kept getting error after error.. (not sure if it was a pathing problem, or installation problem on certain supporting apps)
either way.. I ended up just using a .bat file another member (teletypeguy) posted, and uing the same file structure.
that ended up being this:
on _root of C: drive:
Create a folder called: gerber-files-to-cut
ie: C:\gerber-files-to-cut
INSIDE this directory, you put/copy the gerbertographtec folder you downloaded at the github link above (dont forget to edit it as outlined above)
ie: C:\gerber-files-to-cut\gerber2graphtec
and the .bat file I created/used was this: (use your computer name, not [computer_name]
@echo off
rem This is for printer named "Cameo" which must be named and shared in control panel.
rem This is for computer named "hacker"
echo.
echo This script will send gerber file to Cameo for cutting solder stencil.
echo Generates intermediate files .pdf, .pic, and .graphtec.txt
echo.
echo Set your Cameo blade to 1 and turn cutter on.
echo Load mylar sheet (landscape) at upper-left corner of mat.
echo.
set /p filename= Enter filename of gerber (eg: test.spt or board.gbr):
gerber2graphtec\gerber2graphtec.py %filename% > %filename%.graphtec.txt
copy /B %filename%.graphtec.txt \\[computer_name]\Cameo
This .bat file should be INSIDE of the: ie: C:\gerber-files-to-cut directory.
At this point.. you are ready to startm aking test cuts.
Be warned, this a VERY SLOW process, but very accurate and te results are pretty good.
2-passes, pretty much 'stock' configuration
did NOT cut all the way through!!!.. but looked good (pic doesnt really do it justice as the shadow and it didnt cut all the way through making it look 'fuzzy/choppy'.
Edited to 3-passes
result: still couldnt get the cut to penetrate..(backside was still smooth)
ok.. so at this point.. Im thinking: "Geez, the ULP script and .dxf export from IDLE LOOP looks great right about now!" LOL..
no matter what a BLADE SETTING of 1 wont cut it!.. and the holes never were cut out.
blade setting of two was too much and ripped pads!
but I kept reading around and asking questions, and was informed about the defaults in the gerbertographtec.py script..
(about how to add more than 1, 2, 3 cuts, and the force (pressure) parameter as well!)
This,.. in addition to the tip on shrinking the CREAM layer in the DRC >> MASKS tab, seemed to charge new life into me!
So I opened the gerbertographtec.py script (I also learned you can add these parameter to the batch script, but I think I was more comfortable editing the .py script itself, and commenting out other 'settings' for later review/use
found these lines/values:
offset = (4,0.5)
border = (1,1)
matrix = (1,0,0,1)
speed = [2,2]
force = [8,30]
cut_mode = 0
and edited them...
the only one I really messed with was speed & force (although by default the script will cut a 1" board around your pcb largest area.. you can change this in the border default)
(all images should have the settings used and the results in the image)
Also note that I tried to shrink the CREAM LAYER in Eagle before exporting by 6mil.. and it looked/showed no different than when it was at 4mil.... not sure if it is due to the iTeadStudio CAM file I used to export the gerber files or what?
either way Im happy and impressed with the result so far:
keeping the blade setting at 2..I tried different runs, speeds, and pressure..
here are the results:
At this point. I believe these to not only be usable.. but of 'decent' quality.. (better than the laser ones I have 'paid for perhaps?)...
I am going to be trying the Apollo write-on transparency sheets from the local Home Depot this weekend.
*Project note:
I still get an error/warning every time I run this...
"The procedure entry point ?construct@?$allocator@VVPath@Magik@@@std@@QAEXPAVVPath@Magik@@$$QAV34@@Z could not be located in the dynamic CORE_RL_Magik++.dll"
*****update: by removing the .dll from the directory, this solves the error..
it has to due with either gerbv or pstoedit (I cant re-call off hand).. however I have even tried installing Image_Magik..to get the .dll's and copy/paste them to the directory.. (error persisted)
Love to hear what anyone has on this error and how to fix it!
thanks to all the hardwork and posts of everyone before me and where I source the info/help from!..
its a great 'tool' to have, and a nice ability to not have to source/pay for solder paste stencils any more for hobby/protype work!
update:
at the Dangerous Prototypes forums.. there have been additions done by the members..
* a new .py script hat is optimized for not only faster speed.. but seems to perform better/straighter cuts through the entire stencil/area
* a new GUI for editing the parameters and fine tunign control as been created as well
* Linux and MAC support for the GUI...
IMHO.. this was worth the purchase of my Silhouette Cameo alone..
thanks!
Maverick (Nerf) Mod: custom blaster build log
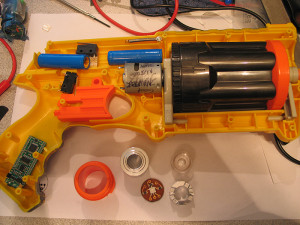
Looking to do a Nerf gun mod... wanted to get some feedback on how to paint/weather it..
found a few projects on-line that I thought we pretty decent.. trying to decide on my own direction here.
1.) black & silver based (techy) theme
2.) heavy metal/blade runner feel (really digging this one and the wooden/brown handle on it)
3.) Army green & black style:
4.) silver & black (mas effect I think? not a gamer).. really like this style too.. even the logo (of some kind) looks right
5.) mixture, black, silver & brown grip..
Secondly.. a few other questions..
1.) how important (cool points?) is that the nerf gun still works as a nerf gun? Ive been thinking of removing the working 'dart' aspect of it.. in favor of some electronics goodness instead?? thoughts?
2.) anyone else have a blaster project in the works??
-----------------------------[update after some work]--------------------------------
update.....
after some work.. I made some progress on this project.
I got the electronics all figured out.. (including making/baking/assembling the board, writing/finalizing the code, home brew/etching two additional custom pcb's...yadda yadda)
It is powered by S.C.A.B...
[kinda my generic/general platform for props..so far I love it]
I think I had posted pics of making my board somewhere before.. (in another thread currently running about)..
here it was it looks like:
here it is on the left next to an Arduino board (with a WaveShield stacked on top of it for comparison)
(fonts changeable on SD card, reads/loads a few defaults off a text file on SD card as well to set a few parameters on the blaster)
*safety = if on.. you need to have the trigger pressed when you boot up
*maxammo = total ammo count before having to reload
*acolor = led color when in auto-fire mode (can be r, b, or g)
*acolor = led color when in semi/manual fire mode (can be r, b, or g)
here is the first video of stage/phase one of the electronics and code development stage of it:
Prepping the nerf gun: (in no particular order)
*I needed a motor.. but didnt really know how I was gonna make it all work.. about torque on motors...sizes..etc..
got lucky and scored a motor that looked like it would fit from my local science surplus store.. biggest I could find that was small enough to still fit..lol (it seemed like it was MADE for the gun once I got it home)
*I knew I need to somehow get some leds into the barrel.. and wanted to have it be RGB..
*Wanted it to reload by pulling the slide on top back
*Since its a blaster the SD card and batteries needed to be accessible without having to open the the gun up (ie: accessible sd card and re-charge port)
*Needed to account for a switch/button to switch from semi/manual firing mode to auto-firing mode
here was my first mock up for testing space and how I was gonna attempt things: (pre dynamic default loading)
(s.c.a.b. in grip/butt)
motor:
after taking apart the Maverick gun (many tutorials all over on it if needed).. I saw how the barrel was turned internally by trigger pull.. and figured Id hack/modify it to suit my needs.
I cut/sanded the hexed shaped top off the post/part that connected to the barrel and turned a little inner sleeve and press fit hole so it would attach to the cut down motor shaft.
before/after motors:
** what you dont see pictured is any pics of the custom PCB I etched for the components to drive the motor (SCAB/Arduino do not have enough power itself to drive high power devices.. so you need a driver/transistor...etc.. something to help out)
but here are the shcematic and pcb files I made in eagle for it:
[img width=568 height=768]http://dmstudios.net/misc/motor_pcb/motor_pcb_2.jpg" />
RGB barrel LED:
I was going to use a DX RGB led star I had laying around.. but then decided it was over kill for a blaster (not like I need to light up a poly tube/blade or anything)..
so I opted for a 505 RGB led,.
*created a custom home etched pcb for it
*turned down a two piece optics holder and pcb 'presser up againster' unit to hold everything.. (similar to Ace's small OD optics/holders... but mine are much more shitty and crude..and no threading....well you get the point).. haha..
I wont go into detail on how I etched.. I have posted a few tutorials stp-by-step on how to make these at home in 10 minutes enough..
after etching.. smear some solder paste.. and populate board with resistors & 505 RGB:
bake it in toaster oven:
make inner sleeve/bottom portion to hold/push the pcb with (incuding some milled out section for wire passing)
make outter sleeve to hold optics in it.. and also has the bottom portion slide in and sandwhich the pcb up against the optics......and fits in the Maverick gun plastic barrel part:
Unit all put together:
Inside the Maverick barrel:
Exploded view of all parts/optics/pcb..etc:
Switches:
Mode select switch.. had to think about where I was gonna put this.. without some huge, ugly slider switch somewhere.. that looked like an after-thought...
I eventually decided to re-purpose the same button/area that used to allow the barrel to swing out and reload the darts..
*(this switch has an led in it.. I am nto currently using it.. but could be used to have the switch backlit.. I have a 3.3v pad on the board)
using a simple lever switch.. for both both main trigger and reload..
reload switch:
this one is secured to some perfboard cut to snug fit for inside the gun area.. it positions it in the correct place so the top slide hits it when pulled back, w/o mod to the top slide area/parts
main trigger:
you can see where I placed it int he above overview shot of the gun layout..
I mod'd/filed down the trigger a bit to hold the lever from the switch it in easier...(works great!)
after getting all this work and aligning things up.. I did a quick mock-up and cram-fu test with it mostly assembled.. (some parts have to wait for final paint and/or assembly)..
I took this video of its current state.. which Im calling 'done'.. and ready for break down and final paint & weathering (attempts) lol
thanks for the poll/feedback..
Im still not sure about trying a chrome/silver/nickle base and some dark washes.. or going with a black base..and trying to silver/grey dry brushing..etc.
(better decide soon eh?) lol
:005:
PoC: Plunger Switch Prototype
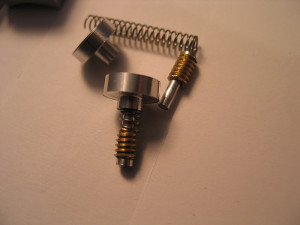
I never posted these... and just recently remembered about them when reading Ace's Obi TPM run thread.
I posted on them..(did a quick sketch while at work to help explain it).. to maybe offer help.. (but no one even acknowledged I posted... boo hoo.. poor me.. right?!)
lmao!
Erv drove into me 'document everything'.. (so here I am.. maybe it'll help fix a cram-fu problem!)
anyways.
I worked on a few different ideas of 'mechanical' switches or methods to trigger latching/momentary switches when I got those illuminated switches a while back..and then again when I started working on 'cores' and all components secure to it (ie: Easterns x-mas gift/x-core..integrated switch)
(Im sure you've seen a few here and there..but I dont think these plunger style ones ever)..
I suppose it depends on your specific application/project but (again) the idea is sound/stable..
yanking the pic I made in Ace's Obi run thread..
for myself,.. these were to serve several purposes.. solvable by either changing the length of the outer threaded sleeve, the length of the 'plunger'...or both. =)
a shorter length threaded outer sleeve lets you thread directly into the hilt...(for switches that are very close to the top of the hilt)
a longer length threaded outer sleeve lets me thread into the hilt..but ALSO my core (or delrin disk..etc)
when I do this..I need a longer plunger end as the switch is usually set deeper and not at the top by hilt/hole.
these are all garage/hacked, home machined..etc Im sure if Ace tackled this, they would turn out much nicer,,and the fit and finish of course would be top notch. (even maybe a lip or something to stop screwing all the way in)
only con I have found so far is its a bit difficult to screw in the threaded sleeve sometimes.. (you need to tape up some needle nose pliers and get to turnin'!) lol
(this is actually how I am planning on finishing my own personal Obi hilt using the bike vale and red button as my switches) (one of these days, right?)
ok just so there is some Proof in the puddin',..another proof of concept..(PoC)
some pics:
part(s) breakdown:
(on top of some TCSS boxes..with some brass and aluminum strips I cut out..same thickness..they turned out good..need to sand edges..and buff)
this is NOT fully screwed in.. but it is also a longer sleeve version.. cut the sleeve in half..
and you can even counter sink/bore the switch end to get it lower/closer to the hilt if you wanted.
see how it works/side view:
shorter plunger see how it goes into hilt to trigger your switch.. of course these are changeable to any length to fit the depth needed.
and not-engaged:
I have two more that are going to go on top of one of these control box.so the switches are on top of the 'cover' and spring like this.
anyways..hope 'someone' enjoys them.. LOL
thanks
PoC: Custom MHS heatsink pcb (for my Obi TPM)
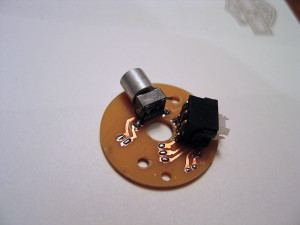
was going to post this in the 'idea thread'.. but figured just make its own thread for it..
another step in my OBI TPM saga.. lol
trying to keep the size as accurate as 'I' can, and still having it be somewhat MHS based at the core...
I was stuck on finding out a way to use the stock switches as real, functioning switches for my hilt.
(Ive always been keen on the all-in-one core ideas... but have the switches on/in the core and some sort of cap/plunger on the outside has always been a PITA for me... here and there a few ideas have came out/been used)
for the OBI.. when everything was done,.. the switch holes would go (more or less) at the same exact level of the MHS heatsink.. so I need to adjust that a bit.. and also find a way to mount some switches in that area..
I had mulled over Madcows switch approach. but just wasnt a good fit..
so I came up with a custom, round PCB, that mounts to the underside of the heatsink..and is secured using the same nylon screws that hold our luxeon star pcbs. (MHS hack!)
here is my prototype..
the bike valve switch will have an SMD led in it.. (like they normally do).. to light up the purple gem in the valve end. I just didnt put it back in yet..from doing the momentary mod to the switch (latching by default)
I also didnt clip the extra leads from the switches yet.. but I believe the idea is sound.. and can open up the doors for others to use the same idea/approach.. (nned to mount a unique switch?.. make a pcb for it!)
I posted a tut on how to etch your own pcbs..etc.. using your home laser printer and photopaper..
1.) make pcb deisgn in photoshop..
2.) print to photo paper
3.) iron to your copper clad board.
you get this:
etch and you are left with your laser printer traces (covering the copper underneath)
remove toner: (pcb is left)
Like Erv taught us.. pre-tin folks!
bend my switch leads underneath..and the other row down:
other switch:
on heatsink:
I dont have a red thumbscrew with the correct threads yet.. but you can see it mocked up there.. (screws right in from outside of hilt)
when heatsink is in MHS part.. it lines up with the holes perfectly.. (cant see it so good in pic_ =(
feedback always welcome..
hope this helps others get past road blocks in their projects!
thanks
The Jeruino (Arduino compatible clone circuit)
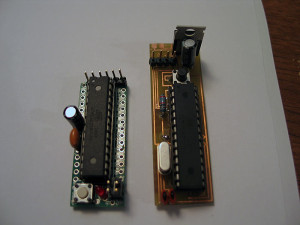
Introducing the Jeruino! (not really.. but everyone else names their Arduino knock-off clone circuit.. figured I might as well be trendy too!) LOL =)
Everyone knows how much of a whore I am for the RFX platform...
I have also been playing with the Arduino for a while too... (any member here or JSSDC can easily jump in..with both feet and be up speed (at least my speed) in a day or so...so I dont wanna hear any pissin' & moanin' about things being too hard.. lazy I'll accept)
a HUGE problem for everyone who posts this junk is 'footprint' going from the non-practical BREADBOARD set-up that is great for YouTube vids.. but not so great for any practical project.. nor is stuffing a 'real/true' Arduino board into a project (they are more development/prototyping and have alot of bells and whistles you dont need in the end) very practical and wastes money.
you can get all the components for a barebones Arduino for around $7 bucks or so.... which is much better than $30+ each time to shove in a stunt or costume or other prop..
I saw Alec post his jedi training remote.. and pm'd him saying that is great project for an RFX or Arduino 'brain'.... since it doesnt need a CF or PC..etc.. this little brains fill a nice niche.
So I opened up photoshop and got to work on making [u]my[/u] first 'real' pcb schematic (IMHO).. since this was a real working board..and not just some traces to hold sensors or switches as I have etched out before..
(I etched another 'real' board...but it was based on TroyO's schematics for a multi-channel LED driver board.. which I've posted before...PWM chopper type)
this one I created myself from scratch.. and google/instructables... (basically ported my breadboard Arduino circuit to a PCB) with the intent being fore Alec's jedi training remote.. (anyways.. not sure if that currently being worked anymore) =(
but I produced my first functioning Jeruino board.. (Arduino clone)
Its no PlecterLabs, professionally design PCB.. etched by a PCB house...etc.. this is DIY at home... (so if your looking for that.. Alt+F4 is for you! =) )
anyways.. on with the story/post.. =)
SO I made a design in Photoshop to illustrate my traces and vias/pads..etc
you print this out on GLOSSY PHOTOPAPER.. done with a LASER PRINTER (not ink jet)
**this happens to be DUAL sided (avoid at all costs if you can..true PITA for DIY)
you cut out your traces/design... lay it over your copper clad board (RadioShack..or anywhere)
and you IRON it.. heating up the toner so it adheres and transfers to the copper board.
let sit for a few minutes.. run it under water.. and rub/peel the paper away under only traces are left on your copper board: (looks like you printed on the board... sometimes traces by the edges do NOT transfer good.. so be careful.)
cut out other side.. and get ready to repeat process:
once you have your traces transferred to the board.. it is time you etch away the visible copper.
All copper is gone.. leaving only the traces you transferred to the board left.
the flip side: (**warning..UGLY.. you can see the lift of the paper and traces that are crummy on this side) (you can see the holes mis-aligned a bit.. but no worries..all good)
this side came out pretty damn good though:
from here.. I removed the toner on the board with some ACETONE..
Next we drill the holes (damn there was a lot)
Doesnt look too bad (from the top)..LOL
clearer view of the bottom side with some mis-aligned holes:
what stinks about the DIY approach with dual sided.. is THERE ARE NO THROUGH HOLES PLATED.. so its a real BITCH to solder through the holes to bridge continuity..
Anyways.. once you are at this point..
you can start to solder on your components:
and....viola`
and finished product..
threw in a Atmel chip from my Arduino.. (already had a sketch/program on it..so I knew it was working)..
powered it up.. BAM.. it worked! (STOKED!)..
however.. before I posted.. I needed to check the FTDI headers.. (these 4 pin headers are how you talk and upload new sketches/programs to the chip to be 'run')...
[b][size=150]FAIL![/size][/b]
it runs...works.. but only a pre-programmed sketch that was/is on the chip.. (BOOOO!)..
who wants to buy a REAL Arduino (besides people like me).. just to swap out the chip for your final project every time your done? (I guess many people do it this way though..as FTDI takes up a little space?)
be nice to just write directly to your final Jeruino..
so after some BS and a few swear words.. I fixed everything..(ala Ultra Sound approach) LMAO...
found a few continuity problems from top-side of board to bottom side of board..
and an FTDI problem...
the Ultra Sound fix was a missing trace to a certain pin (pin7...VCC..yikes)..
so I had to use a fix wire..like the old US boards.. hahaha.. (throw-back)
(it looks worse in the pic)
and of course.. because no good deed go un-punished and hard work is always laughed at in life..
I got punished by NOT doing my due diligence.. doing all this hard work for NOTHING!..
as I found a KIT.. that does exactly what I just created from scratch, myself.. that is MUCH more easier, and much more professional (however you dont get the satisfaction of failing over and over, swearing alot....and its missing any kind of Voltage regulator.. but making a quick PCB for that would be no problem!!!! haha)..
so I got a kit to compare mine..to 'his'... (fucker.. I really like his kits!!)
so without further ado..
some compare pics:
my DIY vs purchased (mine has a vRegulator though..so its a bit longer)
**disclaimer-
I make no implications that I know what Im doing..
that this is the BEST approach
that this is absolutely how things much be done.
I am simply sharing what "I've" done...
but for extra $10.. it can really kick up a stunt or costume..
you have a BRAIN with MANY I/O ports to hook stuff up to..
LED's... servos/motors.. accelerometers... and the list goes on and on..
all the same brain.. just change the code. =)
hope this helps someone finish that special prop/project.
feedback or questions are appreciated.
Thanks gang..
S.C.A.B development…

Over the 'years'.. (since I was first turned on to the RFX project/platform).. I fell in love with the idea of a generic platform for the user use as they saw fit.
motors, leds, rfid...whatever the project was.. a nice, simple, generic platform for users to 'tweak' and customize seems like a great idea to me.
with RFX basically defunct/dead... I turned toward the Arduino platform. Had a huge following, lots of examples.. and quite easy to get up to speed on basics..etc.. (even without an electronics background)
The problem with the Arduino platform (as is).. is that its purpose (to me) is for developing/prototyping your projects.. but not to be used in the end application.
why? due to size.. and price mainly for me.. (although other Arduino variants can come in smaller sizes.. the price is includes extra development stuff you may not use in your final projects...etc... and not to mention a minimal Arduino circuit can be made for under $7.00 bucks!)
And getting an Arduino to play audio isnt done easily (by default)..
****(although now I just tested a super easy PWM based audio output library.. doesnt use any DAC or AMP.. and the quality is pretty decent for what it is!)
SO I began to teach myself Eagle.. (not easy for me unfortunately..but after some time I got more comfortable with it)..
and laid out some stuff.. and finally felt confident enough to start making my own PCB's and having the shipped to me.. (instead of the old DIY home brew etch approach)
So here I am documenting my process.. (and failures) along the way..
a qcuik summary of the things I had to learn.do/involved..
*need to make a the schematic/circuit layout in Eagle
*hope its correct or have others look it over (check against design rules too)
*order the pcb's (sending the exported GERBER files form Eagle to your pcb fab house of choice)
*order a stencil (which is used to layover the pcb and smear solder paste over it to get it applied to the exposed pads through stencil)
*place parts on pcb (tweezers!!!!)
*re-flow pcb in oven
This was my first iteration.. using a different DAC than the schematic I was using as my guide:
Here was my FIRST generation of pcb's I got made:
Here is the pcb compared to other stuff.. an Arduino, a smaller minimal Arduino kit..and I think an US 2.5 board:
here I applied my solder paste.. and populated the board with its components..etc. and re-flowed in my wal-mart toaster oven!!
re-flowed:(done)
I had even tried to fix it by testing jumper wires to the default I/O pins..etc.. (no go)..
Well long story short.. after posting and asking....I just couldnt get it working with the DAC I had chosen..maybe someone else could have?? no clue.. (DOH.. should have just followed along..lesson learned)..which I guess is good.. as I had a few other mistakes as well.. =( SO I started over.
In the end, all I had was a tiny Arduino circuit..with on-board uSD socket.. nice.. but no audio output.
So lets go version 2!!
I got mew pcb's made... got a new stencil made..etc.. and started again.
Here is the process "I" did:
apply the solder paste, using stencil:
remove stencil.. examine paste placement on pads: doesnt need to be PERFECT as the heat from pads will pull solder towards it..etc:
Then populate board: (those TQFP chips are a PITA sometimes!!)
Stick it in the toaster for a bit.. (you can see the solder melt and get shiny)
and when you are done you get a finished board..
Here are some size shots and comparison shots against a full size Arduino & WaveShield (which is what my custom board is together..those two boards in one)
in the last pic you can see some pots wired inplace of some resistors.. I did this so I could dial in not only the volume.. but play with the filter/range, so things didnt sound so muddy/muted..
when done flash the board with whatever code you wrote to control/do whatever it is you need done.
thanks for looking.. was a fun project..
Arduino: WaveShiled build process
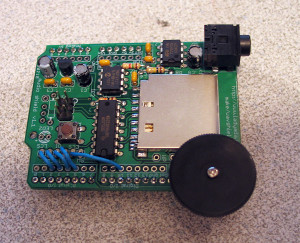
Hey gang-
while I was working on my own custom Arduino based project.. I found myself without a real way to compare the audio output (volume/quality) against the Adafruit WaveShield which I based my project off of)
So I was about to order one.. when I found a guy at my local makerspace that actually had one of these kits. The catch was he had never put it together.
So the barter was on.. I can borrow and test it.. as long as I put it together for him.. (pfft.. no problem!)
Here is my documentation of building an Adafruit WaveShield..
the kit parts:
compare shots against my custom board, for size:
thanks for looking!
summary: nice and easy kit
does what it says in minimal time and effort
volume quality is 'not' that great.. (but they know about it.. and they provide a resistor hack for adjusting the volume)
the filter/range is a bit muffled too..
over-all its better than straight, un-filterd, un-amplified PWM audio! and its only around $20.00
PS.
special thanks to Pete P. @ the local Milwaukee Maker Space! (you guys rock!)
MHS [modified] control box (my entry in cram-fu)
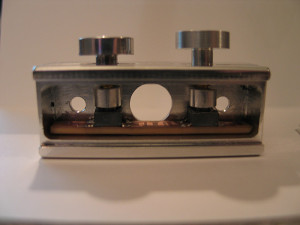
been playing around with a few ideas over the years.. and have worked on a few control box ideas/projects as well...
this one is based off an MHS control box.. with some 'modifications'
things to note:
*has two switches (main and aux) in it.. (one the 'side' of the box.. with custom switches and switch caps/stems
*custom PCB was created for them to mounted, to and mounted to the inside of the box.
*has a 1.3mm recharge port in it
* has custom smd led bar graph (custom made pcb for this as well)
pretty has everything a hilt needs, all located in the......... 'control box'
posting my mock up pics... if things work out good.. (which it look sot be great even).. I'll break it down again.. re-fine...and buff/polish and powder coat for the finished product.
hopefully this gives some ideas for everyone else... make things work for you!.. make what you need...
lets begin:
1.) take your favorite drawing app and make a PCB design.. no special tools.. draw BLACK lines/traces and pads where you want 'copper' to be..
get your copper clad board/section..
2.) print out image on glossy photo paper.... iron/transfer image/toner to the copper board.. rinse under water to remove paper.. soak in etchant to remove exposed copper:
3.) after exposed copper is gone.... use a q-tip and some mail polish remover to remove the toner from the pcb... (revealing the copper/pcb under neath)
***(all this above has been posted many times before.. and shame on you for not trying it!... this could have saved your ass in that 'one' project!) =)
4.) mounted my modified switches to their PCB.. (these have the threaded tops on them for external switch caps to be used form outside the hilt.. keeping the main core/chassis/box internals standalone)
several solder pads depending on the need/space available
5.) mounted (mocked up) in the control box:
6.) (although it looks 'off' its really just the pic.. things line up great!)
side view of holes and where the switch tops are
7.) top (custom) pcb made..for the led bar graph.. (this posed a problem due to space.. and the fact that I wanted each led to be addressable for either all direct drive..'or' for CF led.txt sequence..etc.. not to mention trying to do double sided board without through hole plating.. (making my own)..
again.. space was concern.. (both sides)
I think an led (possible two) got ruined by heat? or something.. but Im going to replace them real quick. (as they only light up partially)
in the end it will be black box.. aluminum top plate and aluminum switches on the side of the box.
the top 'smd led bra graph' pcb/portion
this is where each resistors goes: (bottom of board)
quick mock up:
(again the switch pcb is in place already.. the custom pcb's are almost forming a box to support each other
---------------------------------------------------------------------------------------------------
got a couple hours the other night to finish 95% of it up... (I think 'real' professional PCB's would serve best here)
got the bottom half of the bar graph competed (resistors soldered, wires soldered..etc)
used 1206 resistors.. all I had at the time.. (yesterday my 0603's came.. had I had those in my plannign stage..I think everything might have been topside mounted....oh well v2 I guess..lol..this is my PoC)
still not quite sure how/where to tap the V++ to.. I have a few ideas...not a big deal though any place will work)
quick test of being lit up.. (had to replace 2 leds as I think they were 'damaged' by initial placement? maybe soldering too hot? different bin? one was of color.. when lit up bright..then gradually died out after a few seconds)..anyways replaced them
2 x green
2 x yellow
3 x red
each resistored, each individually addressable... (so can be direct driven, used with CF, or as PLI) =)
quick mock up of the side/switch PCB inside the box. and the switches/caps/stems I made for them.. (still need to be shortened a bit..but they are close enough to work and show the effect/style)
more pics of the 'switch caps/stems'
the pcb's took about 30 minutes total to make.. (probably another 15 prior on trial and error on printing out paper copies and doing size checks)
now that I feel the idea is 'sound' I'll go back and plan it out a bit better.. (this is supposed to still have recharge port added..but Im not sure after implementing things this far it will make the cut)
time to break it down.. pc the control box BLACK..
buff/polish the 'switches'...
and complete the 'top'.. which is an already sized aluminum strip that sits flush like any normal 'card stock'
there is NOW window cut/milled out of it yet through for the bar graph.. =(
enjoy.