AoF Pommel (mod)
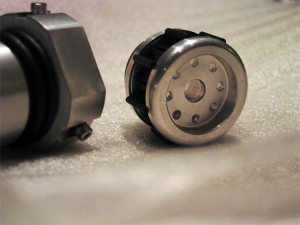
AoF Pommel (mod)
Got some pommels made from Randy a few (years?) back now...
they were oversized (OD).. because most MHS pommels were stock OD..
it is very similar to the Jay-Gon pommel #10 that is in production now..
I like them because:
a.) using a shroud/sleeve/overlay isnt BIGGER than the pommel OD now..
b.) it helps 'lock' in overlays because they cant slip past/over the pommel..
You can see an original one on the right...and the mod'd one on the left.
(some turning down..and trimmed up t-track)
on a hilt/extension section:
Close ups:
R&D: Proof of Concept bearing chassis/core mounts

Being as its winter here..and I doubt I'll get in the garage much, anytime soon..
Wanted to post this idea/concept I had in my head..
while the pics are of a 'core/tube' type chassis this same concept could be used to an open 'sled' type chassis as well.
I talked about this with Fender a bit as well.. although the reverse sound one is not 'pictured'..
I think the idea is sound.. and this is just a roughed out idea..(including the cuts!!)
Im sure someone can tweak/fine tune.. find a better way. (in theory, a bearing wouldnt even need to be used..but makes it smoother)
Pros:
nice way to secure your core/chassis to your pommel for easy removal
no twisting wire problems
Cons:
mod'ing the speaker holder is PITA.. because the stock speaker OD is big.. I ruined s peaker mounted.. and that one pictured 'was ruined' but salvaged..lmao
in certain pommels, it wont work. (to close to end for insert)
not a lot of resonance
Together view: (not in pommel...but a possible end result could be)
Here is I have my 'core' (main tube) that can hold soundboard & batteries.. the top portion is just added from another past project.. (but is one possibility)..
that top part also have a bearing in it.. and can 'spin'
The 'main' part..(together)
The main part(s) (what is consists of)
turned 'stem' to fit bearing.. (can see similar in background)
Bearing got on stem..
I cut a piece of some external threaded tubing I had NPT 27 tpi I think?.. hollow..
that is actually press fit on there..and is not coming off.. but could be glued just as well little dab only..
it helps keep the bearing in/down... and the threaded part is used to secure the back of the MHS speaker mount.. (NPT 27 tpi tap...I'll have to look up exact size off hand)
the MHS speaker mount is turned to OD that fits INSIDE the pommel ID...easier to just bore out the pommel a bit though to be honest..save your speaker mounts from being wasted..lol.. hard to leave a 'wall' to snap the speaker into
there is a 'ring' with the ID of the bearing OD.. and the OD of a pommel ID
this slides over everything (stem, bearing, NPT secured threaded end)..and has hole tapped so set screw locks ring to bearing..
now you have your free spinning 'ring' that the pommel makes contact with..leaving the speaker/mount secure/non-moving
you get this:
the speaker side.. (see how its threaded through)... maybe dab of glue too?
alternate pommel (still works)
off-topic:
Here is the top portion.. (although a bit off topic)..notice similar 'stem/bearing' system..
but this time a top part goes over the bearing.. (set screw secured to bearing)..
and it spins the crystal, etc..
back on topic:
ok..so you take the whole thing..after you secure the 'bearing mount' to your core or chassis...etc..
and it slides into your pommel.
you can see the little drilled & tapped hole in the pommel.. un-obtrusive.. and it secure the pommel to the 'core'..make sure you secure it to the 'free spinning ring'.. and not the speaker mount..
side view:
feed back always appreciated,..
Im sure it can be improved upon...so thats why I shared it..LOL
maybe not for every build..but if the case calls for it..here is one solution to apply.
Thanks
Custom/MHS OBI-TPM (hybrid)
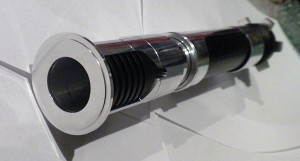
ok..so this has been on the burner.. for....well for a long time actually.. I sorted started it when I saw Obi-Dar posted his build start...
it was shelved.. as I didnt care for the route I was taking at that moment....
anyways did some more work on it.. and here is where I am at.. figured Id get some feedback..
I think it looks a bit 'weird' to me because there are no cut-outs in the shroud/emitter yet..(Im hoping thats all it is!..lol)
as far as being an 'exact dup' in dimensions.. its of course not.. (its no ACE OBI TPM to be sure, spot on with awesome machining) .. 'but'..its not that far off from the dimensions I got on-line.... the most notable place is the main hilt 'OD'.. which will mostly be cut away so I dont think it will have that much effect on the final look... every thing else is exact or a not 'too bad'...
overall length is over 11".. but little under 11.5 if I recall..
feedback is appreciated of course. things/areas to work on.. (although its not complete of course).. or things that should be re-done perhaps?
Thanks.
(Im no photographer!)
The parts used:
1 x Ace Obi TPM pommel
2 x 1.5 sink tube adapters (turned down to be 1.39 OD and faced to be roughly over 1")
1 x 1.25 'core' aluminum tube so it has a 1.25 choke section (slightly modified to meet ID of one of the adapters I used)
1 x MHS BH #3 turned down to be 1.39 OD)
1 x custom hilt shroud ID bored to 1.39...OD to match the TPM as best I could..
1 x custom shroud ring/support for the top end which has a bit larger OD and design
1 x custom emitter shroud ID bored to 1.39 (OD has a bit of a lip/larger OD than the rest for the 'top ring")
1 x custom 'ring' taking a cue from Randy/Obi-Dar's build of course.. (and because I fubar'd my 1 piece attempt the first go-around) (DOH!) :dft001:
All parts
Rings attached:
Top section:
Side:
Angle:
Full:
Last:
The OD of the ring needs to be opened up to 1" to accept a blade still.. but thats really only about 10 minutes of work to do..
if it passes the test(s).. then I'll work on the shrouds or something.. wire it up.. and see what board it gets (if any)..
if it goes over well.. I always have the 'rule of two' for builds.. and there is parts to make another
Thanks gang.
-------------------------[update II]------------------------------------
just some quick update shots:
got the 3 windows in the top emitter shroud and the window in the grip shroud cut out by Tim (great work too, thanks Tim)
bike value
some bezels
and the delrin 'grip section' and I can focus on internals..
not sure if it will be than board/battery pack etc...
not too much room for a chassis!
some pics.
(I think she is turning out very nice.. no "Erik/Ace" version!..lol.. but nice to me!) and not too fat/chubby.
the shroud and BH fit like a glove.... and Tim's window cutout make it look so nice.
I put the lines/grooves in just about the perfect spot with the BH and the modified adapter 'seam' makes it less noticeable
Heres a pic with the ring on and all together.. (pic isnt so great..its look nice in person.)
more pics of the sleeve I turned down..with slight dip/bevel that i sent to Tim to be cut out.
A pic with the sleeve and the 'collar/ring' for the 1.25 inner and sleeve connector/support. (this part is being re-done for better tolerance fit....that god its not a hard part at all!..)
Some side/full length views:
no delrin inner grip section.. just a 'temp' all black filler...lol
hopefully I'll get some free time to wrap up the hilt stuff.
Thanks
xCore: #2 (Green Lantern) aka: Eastern57 x-mas gift
Eastern xmas gift (copy of same proto system above)
I have a couple more variations on the modular sections/parts..
appreciate all feedback...
specifically on things like:
switch mount/bucket
*standalone vs. part of heatsink bucket
*generic enough for all switch types or maybe 2-3 yes?
battery/sound/speaker bucket:
*size constraints? stuffed 2xAA sized batts and a US2.5 in there.. probably some room for wires..not much else? (not sure of CF would fit due to height.. maybe different battery solution?)
*make both speaker only bucket and attach battery/sound board to 'rods'? or other area? and the speaker/battery/sound bucket? or just the former/later? (maybe milling out some grooves in the bucket will help with space a bit?
heatisnk/led bucket:
*right now the led/heatisnk is part of the 'core'.. should it not be? shoudl there be an alternate 'modular' section you can choose as an 'end cap' to the core?..and then you just run wires from core to led, like in any other normal build?.. of course you would have to choose to either lock/secure the core using the speaker mount end 9liek in normal MHS builds using a pommel speaker mount...or an end cap/section that has the OD of the heatisnk..and using that approach to locking/securing the core to the hilt?
Eastern will be giving a review of his as well when he gets some time to play with it.... maybe covering some of the topics above .
Thanks
Custom MHS: “trim ring-sleeves”

Ive been kicking around this idea for a bit..and actually got started working a few POC's..
however I just dont think they will get the fit or finish or really the customization and coolness 'reached' if these are done by myself.. they need Tims new CNC stuff or ACe..somebody to make them 'top notch'..
such as taper or other mill work..
I think I can only do a few 'styles' with my tools.
anyways.. I tried to explain it to Tim.. but a picture is better..
it follows sorta the same principle as the trim rings do.. the ID is just bit enough to go around the male threads..but not big enough to go around the OD of the MHS parts.. (hence being locked/sandwiched down by the two parts)
well instead of a 'ring' how more of a sleeve.. for decoration.. longer/bigger bezels for switches.. or cut outs for switches..
use them at top or bottom (pommel side)..and pretty much reversible.. could be purely cosmetic.. or functional..
thoughts?
-------------------------------------------------------------------------------------------
Here is one of the P.O.C's (proof of concepts) for my mhs add-on, dubbed, accent trim..
this is only one..but I displayed in both a 'header' and pommel piece/usage.. and I think I really dig the pommel way..
anyways.. no mill or cut out for buttons/switches on this one.. but I think have TWO of these would balance out any hilt nicely.
also.. since it locks down by the pommel or BH or whatever female threaded piece.. you could use an additional set screw to secure it..
and you could have a rotating/sliding 'cover' to display/reveal re-charge ports.. xstal chambers..etc..
anyways.. on to the pics:
the solo part I made:
Mock'd up on a saber/test hilt:
as header:
Mock'd up as a pommel:
Quick little add-on of brass ring 'section' to spice it up..
and a size/perspective/overall shot to see how it comes together..
feedback appreciated gang!
overall I, myself am giving both the BH mod with shroud project and the MHS accent trim project passing grades.
I feel they are quality additions, that do NOT take away from MHS, utilize its parts still along with custom parts and customization to make things unique, adding depth and personal choice/taste
I also think these are mods that will add to your final price point when selling.. as they are 'new ideas' will havent 'caught on' yet, and many of can do here.. or have done without it taxing anyones wallet..
with Tims new CNC engraving and mill work.. these accent trim parts and shrouds should be getting some special treatment!
thanks
DIY: Homebrew PCB etching
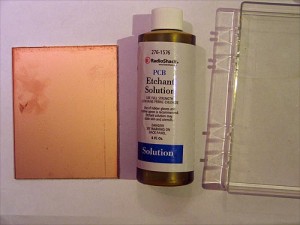
Not sure how many (if any) of you may ever need to do this...
but if you want to mount those sensors we got or accent leds..(or anything) to a little custom PCB for your projects..
you can make a PCB all by yourself with nothing more than a black-n-white laser printer, the copper pcb board, and some etchant solution
Etchant Solution:
http://www.radioshack.com/product/index ... Id=2102868
I think they stopped making them..but some stores still have old inventory.. (I got my last 2 kits for $3+ each)
# 276-1576 is the KIT# (read the description, and you'll see reference to the kit)
comes with:
etchant solution
tray(s)
etchant/ink remover solution
copper PCB board (2 thicknesses)
drill bit
scotch brite pad
permanent ink marker
you really only need the etchant and the copper pcb board.
I made a little layout/schematic (nothing special)
in photoshop.. @ 300 DPI
** make sure you print on glossy PHOTOPAPER.. this works best in my tests..
print out your schematic..
cut out schematic
iron schematic to the copper pcb board... let it sit a bit.. make sure transfer is nice.
under cold water.. 'wash away' the photo paper on the PCB board.. it will leave behind the INK/TONER from the paper on the PCB..
(I didnt take a pic of this....sorry)
but it would be like you printed ON the PCB (more or less) after you wash away the photo paper with water.
fill tray up with etchant solution..
throw section of pcb board with print out ironed on it..into tray..
(etchant will eat away/remove ALL copper 'except' where the ink/toner was left at)
once all copper is gone..and only black ink/toner is left on board...
you can take high grit sand paper or the scotch brite pad..and clean off the toner that was left on the board.. revealing the copper (now traces) on the board..
It can be used to get some fairly decent lines and things are very crisp for what it is..
I made a 'pcb' board to hold my X & Y axis swing sensors....and my clash sensor.. and soldered solid core wires that fit into my bread board to test with the RFX project..
Ive also used this method to make a few LED driver boards to drive a LUXIII/P4 w/PWM support... as well as a 3 & 4 driver board for RGB or RGBA diode LEDS..
I made these printing on WAX paper though..and the transfer isnt as good after ironing as using glossy photo paper and washing it away under water after ironing.
and these are just HOME BODY, DIY needs..and they work a treat..
image how small things could be if they were professional designed and manufactured!! PHOOK!>.lol
hope this helps any of the DIY builders out there..:)
-----------------------------------------------------------------------------------------
For these tests...
I have used a very affordable HP LaserJet 1022n (n = networked)/
basic stock black-n-white laser printer.
as for photo paper.. I have success with several brands, sizes & type.. glossy or semi-gloss all types were..
all transfer CLEAN, SOLID lines..vs. using a wax paper or a mailing label backing or similar..
I was very impressed with the quality of transfer using photo paper vs. anything else.
re: etchant.. a few other things to note..
myself. (wrong or right).. I keep my solution in a plastic tub/container.. (with lid)..and just leave it.).. I re-use it.. sometimes adding more or etchant at times..
also adding air/bubbles to the solution helps speed up the process and works well...
my point/goal was to provide a method that doesnt require any special ordering of materials or supplies.. everything should be able to be purchased locally...for cheap!
Joe Jedi Control Box Use: 2

Im always looking to re-use or hack existing parts.. MHS.. heatsinks..whatever..
I had originally played with these control boxes and mounting a PLI in them (dimensions are almost spot on)..
I never have any 'cover' on them..and they looked a bit 'steampunk/unfinished'.. (not the type of fit & finish "I" like)..
may a few.. and was done.. other day.. got back to working on one for a buddies MHS OBI I am making him.. (no clamp.. just this contol box)
I figured Id share for a few reasons..
1.) it actually came out fairly good.. I made a black one and a 'brass' one..
2.) anyone can make these..no special equipment needed
3.) makes use of old or existing 616 parts..
4.) total was really only a few bucks. (@ your local ACE hardware..some brass flat .99 ..and a 'brass channel' $2.49)
this may get a PLI mounted in it as well..
and the cover will get a slit/slot cut out in it for the leds to shine through..
alternatively.. you can put fill in the sides where I am mounting switches/buttons.. and keep the space under the cover blank/empty for switches..
"OR" see the GHETTO PCB 4 U thread..and make/etch your own PCB and fake resistors and diodes..etc.. and mount in it there..like on the OG graflex's
(and I also posted a pic of an OLD AoF pommel I had two of..that I modified.. and added in some 'rubber grip' pieces..
Front.. close cover:
Top cover open: (bottom has holes to run wires) (you can see both slider switch and mom. switch on each side)
Side:
Slider Switch side:
Mom. Switch side:
AoF Pommel mod:
Since I have a few of these.. I have some without the switch stuff cut out..
but I was thinking the slider switch will be for the PLI...
*always on (unless kill key is in of course)
*off
*on when saber on
Be cool to fit in battery in there! pop it out to charge it up..pop back in!..
anways.. this thing is a space saver fits on the outside of a 2" extension piece..
single (middle) point mounting, means no worries about using it at top under a bladeholder/heatsink
feedback is always appreciated.
Thanks
-----------------------------------------------------------------------------
oops.. the pics..
-----------------------------------------------------------------------------------------
also...one more last pic... before final steps are done..
quick mock up of the PLI inserted..
not fully installed..(you can see the wires still)..
but you get an idea of how it'll work & fit.
you can also see the new 'cover' I am making for it.. to let the leds shine through..
--------------------------------------------------------------------------------------------
I think I might have to re-do the sides (again)..
the problem at hand is how to get the PLI to sit a bit LOWER in the box..
I have a few options..but none will really gain me MUCH more space in lowering it..
alternately..re-doing the sides and making them a bit taller would work.. but will it throw off the visual looks of it with it being taller and not 'as' flush?
anyways.. anyone/everyone can make these..
takes about $4.00..but you should be able to make 2 out o the materials..
At my local Ace Hardware store.. (just like everyone else).. we ave a little Brass/Aluminum/Copper section for hobby metals..robs, tubes...flat/sheet...etc..etc..
one of the pieces they have is RECTANGULAR tubing.. not very wide at all..but a few random sizes..
I grab one of the bigger pieces..and then the FLAT brass strip you see in the pics..
cut it long ways....and down the 'vertical' axis..not the horizontal.. (see pic)
you'll be left with two pieces like this:
_ _
| |
| |
| |
| |
- -
you dont need the bottom 'lip'.. so shave/and it off... so you're left with an upside down "L" shape:
_ _
| |
| |
| |
| |
thats basically it.. LOL
make another set just liek this.. but make them SHORTER (not as tall).. so just sand/shave down MORE wen taking off that bottom lip.
this is the basis of your 'shelf' system.. so you can slide the brass cover into place..
_ _ _ _
| - - -- |
| | | |
| | | |
| | | |
you can then do the same..of course smaller width.. for the 'width' of the box..and to keep the 'sides' secure and not loose.
---------------------------------------------------------------------------------------------
ok.. to finsh it up more or less..
the PLI cover/cutout window..
my question to you guys is:
to secure the PLI...
should I:
a.) try and use some screws/bolts to lock the PLI down?
Id of course like to do this UNDER the cover.. but if not..might have to go THROUGH the cover.. ending the removable/sliding aspect of it.
b.) raise the sides a bit to compensate for the 'thickness' of the PLI?..then I can mount the PLIS down.. glue or secure the sides in.. and the cover can be removable?
sorry about the finger prints.. did a quick buff on the pieces to take a pic for YOOUZZ GUYZZ..
Joe Jedi Control Box Use: 1
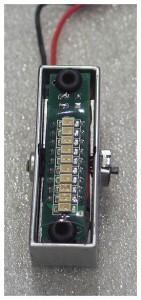
I have been working on a few PLI housing/control boxes for some of my builds..
figured Id share the latest mock-up/model with everyone.
this isnt perfect..but its a mock-up.. I have a few that turned out nice.. black & silver also, with & without 'bands' style..
uses the PLI from the store.. and fits perfectly..
mounted a mini latching slide switch (DPDT) for the main power..
on this particular pictured...(since I am testing out a layout to be used with a Plecter Dimmer) sports a momentary tactile button on the other side to set the options of the board without having to be 'inside'. (personal preference really)
but could be anything, or used for whatever AUX you like.. instead of a slide switch I have also mounted a few momentary push buttons in that area.. with some 'covers/caps'' (they look nice)..
what you dont see pictured is any covers.. still working on a few.. nothing Im super stoked on.. the LEDS are off-set and not centered.. so its hard for me to find a balance in the cover design with what I have found so far.
My idea is always to make things FUNCTIONAL and look clean/smooth in all my designs/builds.. this lets me house MANY things without much worry about where I need to drill holes in my MHS parts...:) its just one whole to get all wire through.. the hole on a pre-drilled hilt is plenty big for example..
I have also made other version of this that DO NOT have a 'real' PLI.. but in fact just a strip of colored LEDS.. (looks great..but is just eye candy/accent LEDS).
I was hoping Jay-Gon-Jin would have come up with some thing like this on those brass runs he did.. they were sorta close.. Also surprised there isnt any 'parts' like this available in the store or other 'outlets'..
Custom MHS BH #3:
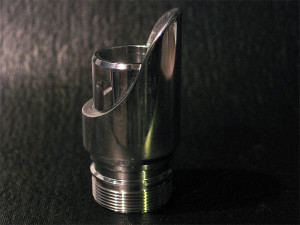
I posted asking a few questions on PC'ing..
this was inspired a while back from Big EZ's Tactile build.. (which seems to have been a trend lately)... but was supposed to have a 'trigger guard' built in..
it does.. but Im not 100% happy with it.. (taken from a toy gun from my kids).. looks 'ok' after paint (maybe better)..
I have one more guard I wanna try (hoping it will fit better or a mount solution will reveal itself to me!)
anyways..
here are some pics of the WIP build..
modified BH
custom shroud
v-groove
3" extension (modified)
stock MHS pommel
I also fubar'd my 3" extension.. (pics below)..LOL
so I need to grab another off the bench and mod it again.... goes to show.. do NOT PUSH the amount you can turn down an MHS part! (especially by the threads!)
anyways.. figured Id post a few pics.. and what NOT to do to your MHS parts! LOL.
before I messed up the 3" extension:
Broken piece in place:
all three mod'd BH's with custom shrouds (3 so far...and I think last..I have 3 'longer' versions that are similar to a 'graflex' top in length (not quite) that go over not only the BH's..but part of the main body as well..... too bad it'll be seen as a rip of Slothfurnace graflex build that uses it...cause the firstone is very similar.
some other junk too.. my first red/sith build (bottom)
and an attempt to make a 'clean'.. future'ish saber.. very clean..nothing but liquid chrome 'look'.. (working on the MC type buttons..but a bit more 'recessed'
and my mistake: =(
any thoughts or ides on the trigger/guard is appreciated.. Im really NOT digging using plastic or salvaged from a toy.... but not sure what else?
-----------------------------------------------------------------------------
I PC'd it..
as well as the v-groove..
still on the fence
1.) do I remove the PC from the 'ribs/nubs' on the v-groove? (and pc them trans gold?)
2.) do I do everything that is in bare aluminum in trans gold? (nubs and BH..and pommel)
keep in mind the 3" exntension is there as a filler..cause the other one broke.. needs to be turned down still.. and some visual mods/grooves added..
that will also be black.
suggestions on 1 & 2?
sorry only one pic ATM... the others were kaka..